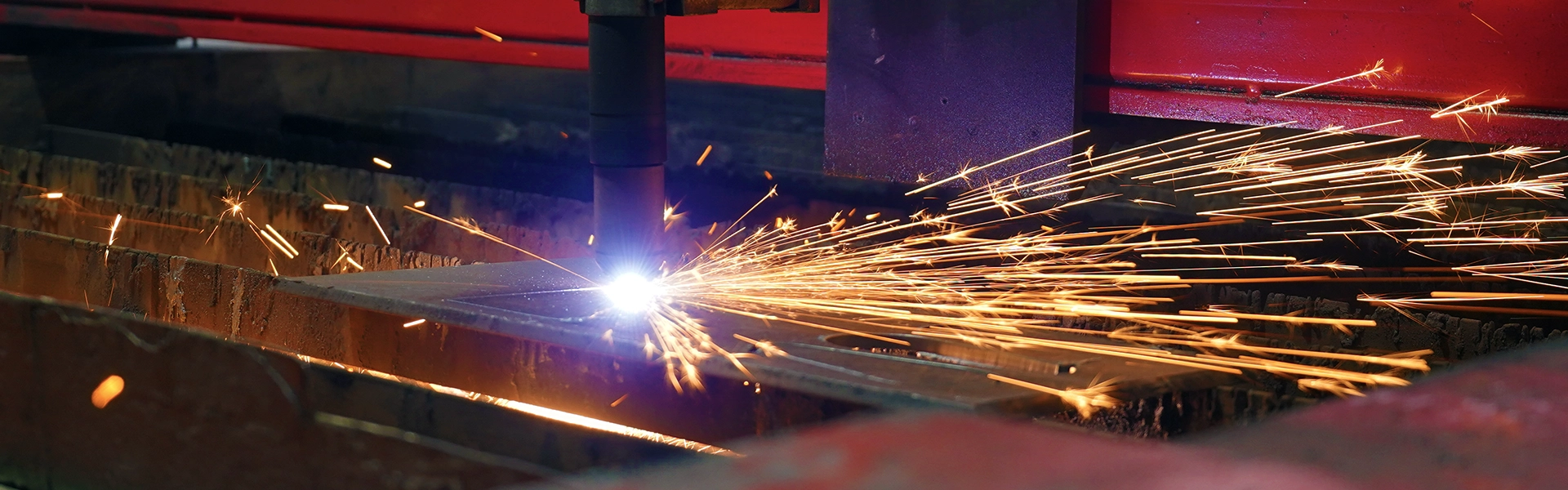
WORLD-CLASS Parts Production
With 30 years of experience in advanced automotive parts manufacturing, Autogroup International provides safe and high-quality left-hand to right-hand drive vehicle conversions. We use reverse engineering design processes, component prototyping and material testing to ensure precision, quality and conformity. We adhere to ISO 9001:2015 Quality Assurance ensuring rigorous production and quality control standards are applied on every component. You can trust Autogroup for reliable, high-quality parts that meet precise production specifications for many years to come.
Vehicle Specific Design & Development
Each of our right-hand drive converted vehicles require specific design, development, prototyping, testing, mold making and production of many parts designed to meet high quality & safety standards, vehicle performance requirements, while taking into consideration the physical space limitations of the converted vehicle.
Quality & Conformity of Production
The safety, performance, and reliability of a converted vehicle depend on the quality of each component and its conformity of production. Each part undergoes meticulous design and rigorous testing to ensure that every component has the same material properties, performance characteristics, and safety standards.
Replacement parts
Our vehicles are backed by a 3-year warranty, ensuring that we have replacement parts available or the ability to remanufacture any part that requires replacement. This commitment requires us to maintain a significant stock of parts and adhere to strict production conformity standards to remanufacture any necessary parts throughout the vehicle's lifespan.
THE DASHBOARD
A vehicle dashboard is made up of around 40 different parts, some of which are visible and some not. Certain parts, including air vents, display screens, instrument clusters, airbags, and switches, are reused while many need to be reverse-engineered using advanced 3D scanning technology. These parts go through rapid prototyping before being manufactured through 3D printing, fiberglass, or plastic injection processes. Several design and production elements are taken into account when creating a new dashboard component, such as the component's physical properties, including its structural integrity, whether upholstered or not and also its UV rating must be considered.
THE HVAC SYSTEM
Our team needs to fully reverse engineer the Heating, Ventilation, and Air Conditioning system as the blower and distributor units must be relocated from their original location on the right-hand side behind the dashboard to the left-hand side to accommodate the vehicle conversion. To achieve this, a combination of reverse engineering and mechanical engineering expertise is utilized to design all the necessary modifications to the HVAC system. Prototype designs are tested using 3D printing technology before we proceed to manufacture both plastic and fiberglass components.
WIRING LOOM
The Electrical Engineering team and auto electricians work together to redesign, modify and test all wiring looms, which include the main loom, door switch loom, dashboard loom, engine bay loom and seat control loom. This is done to ensure that all components function perfectly after the conversion process. All wiring modifications are then independently tested as part of our Quality Control processes to meet ADR regulations.
DOOR SWITCH PANEL
As part of the conversion process, it is necessary to change the door switch panels on both the left-hand and right-hand side of the vehicle. This involves a complete redesign of the door switch housing, which includes 3D scanning of the original OEM housing and then reverse engineering to create a new right-hand side housing that can control all four windows, and a new left-hand side housing that can control one window. In addition to this, modifications need to be made to the wiring loom to allow for the control of the windows from different sides. The PCB also needs to be modified to adjust which windows each button controls.
SEAT MODIFICATION
During the conversion process, all vehicles need some degree of seat modification. This modification may include relocating seat control switches, in-seat massaging, heating and ventilation from the left-hand driver's seat to the right-hand driver's seat, and repositioning seats to ensure a correct driving position. In some cases, reupholstering the seats may also be necessary, depending on the client's requirements. This is especially true when a custom or bespoke interior is requested.
STEERING
Autogroup International has designed, developed, and tested a new right-hand drive steering system for all vehicles that undergo conversion. Collectively we have over 30 years of experience and significant mechanical engineering expertise in steering gearbox, hydraulic rack and pinion steering systems, and electronic power steering used in new EV vehicles. With this expertise, we can develop the ideal steering solution for each vehicle platform converted to right-hand drive.
3D PRINTING
The latest 3D printing technologies such as small and large format stereolithography (SLA), selective laser sintering (SLS), and fused deposition modeling (FDM) are widely used in vehicle design. These technologies enable rapid prototyping, creation of masterpieces for molding purposes, and printing of final production pieces.
PLASTIC INJECTION
Autogroup International has nearly a decade of experience in utilizing Reaction Injection Molding (RIM) to produce both small and large plastic components including parts for dashboard and center consoles. We have perfected the use of RIM plastic technology to create mirror-image components with identical characteristics such as rigidity, external finish, and UV protection levels for many of our key conversion components.
FIBERGLASS
Our team of over twenty-five fiberglass technicians, including a small team of highly experienced pattern makers, has been manufacturing high quality automotive components for the last three decades. We specialize in producing right-hand drive dashboards and have perfected the art of developing the initial 'masterpiece' dashboard, creating molds from it, and manufacturing all the required fiberglass components for each vehicle. Many of our pattern makers have been with us for over twenty years, bringing extensive experience to every project.
UPHOLSTERY
The Upholstery team is responsible for the most visible production task in a complex right-hand drive conversion. They focus on upholstering the visible components of the dashboard, center console, door panel armrest, and other panels to ensure a perfect match to the original OEM trim. This includes matching the color, texture, and feel of all upholstered parts.
WELDING
Our expert welding team is responsible for all metal fabrication tasks, such as manufacturing the dashboard substructure, modifying the firewall, creating the wiper arm mechanism and mounting brackets. All these tasks are designed using the latest CAD software tools by our Engineering Design team. Moreover, the welding team is accountable for all vehicle armoring work for up to B7 protection levels, roof lifts on SUVs (up to 6" higher roof lift) and other fabrication work required for our specialized vehicle projects.
LATHE & MILLING
The Lathe and Milling team produces various components, such as bolts, hose connectors, bushes, and couplers, needed for vehicle conversions based on the plans and specifications developed by our Engineering Design team.
CNC
The CNC team utilizes both 4-axis and 5-axis CNC lathes and steel hardening technology to manufacture specialized steering and firewall components for various converted vehicles. The Engineering Design and Mechanical Engineering teams complete all designs for the manufactured components, and a 3D printing prototyping process is conducted before the products enter production.
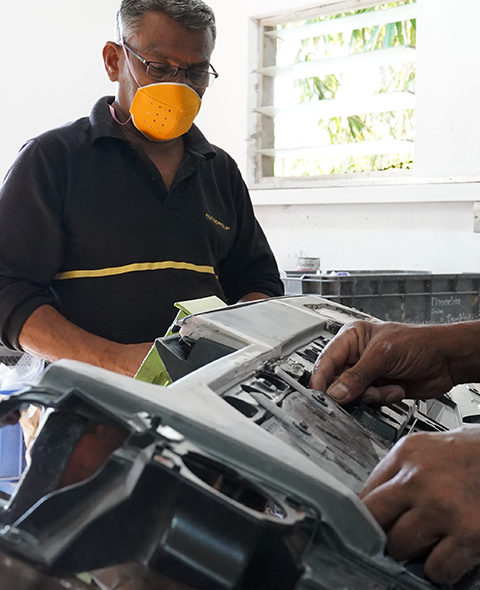
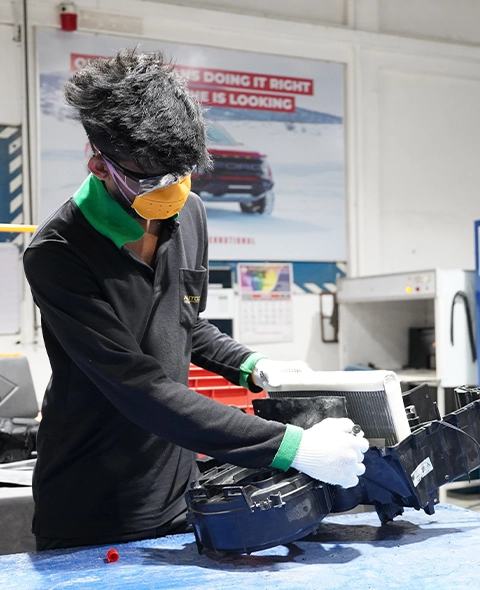
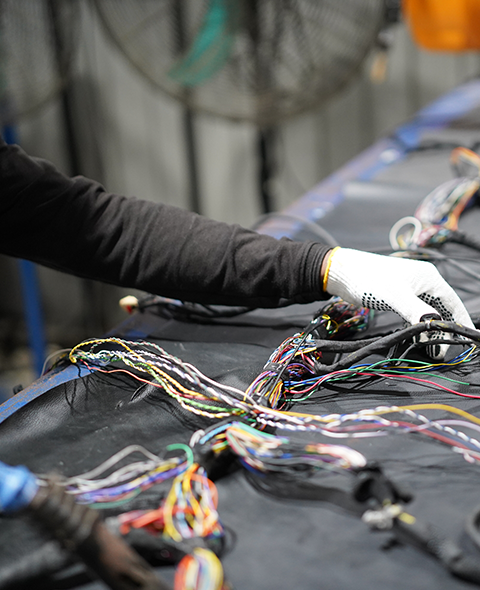
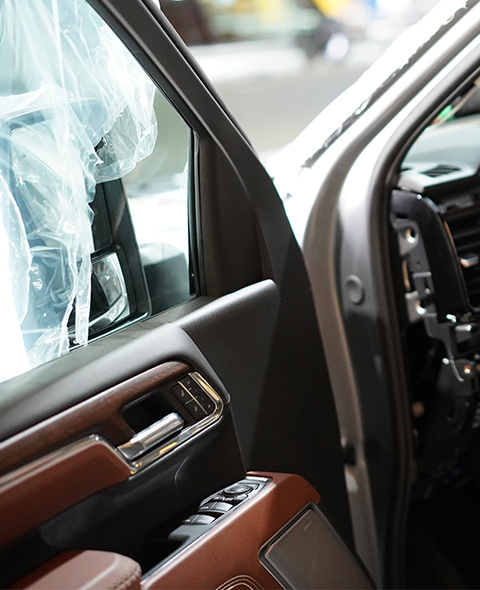
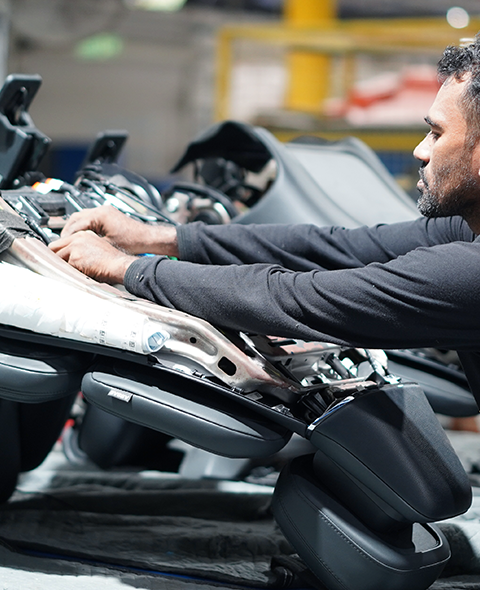
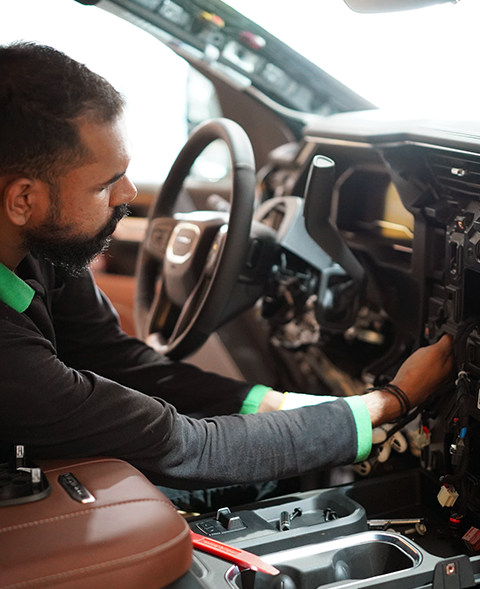
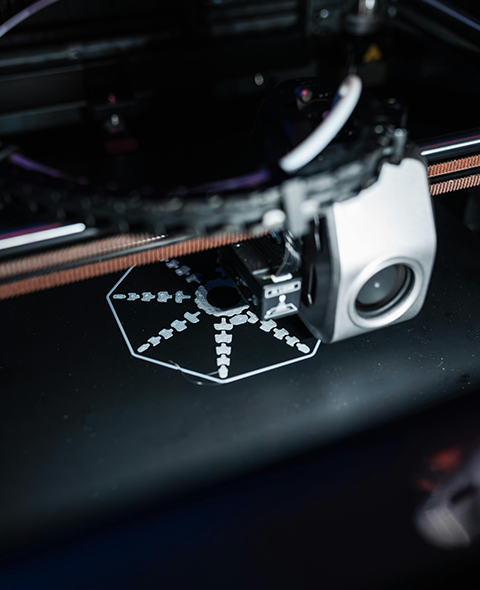
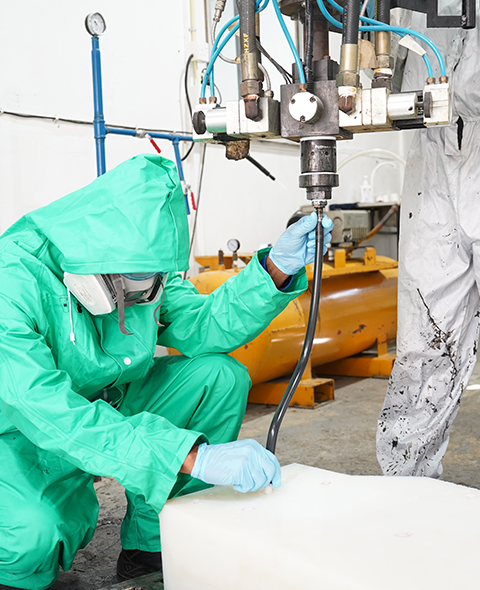

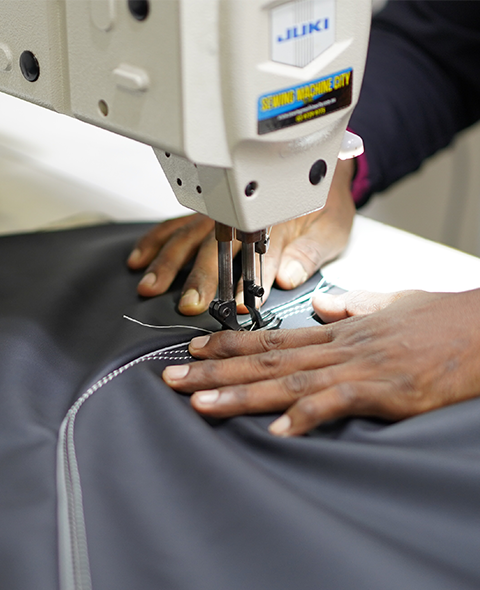
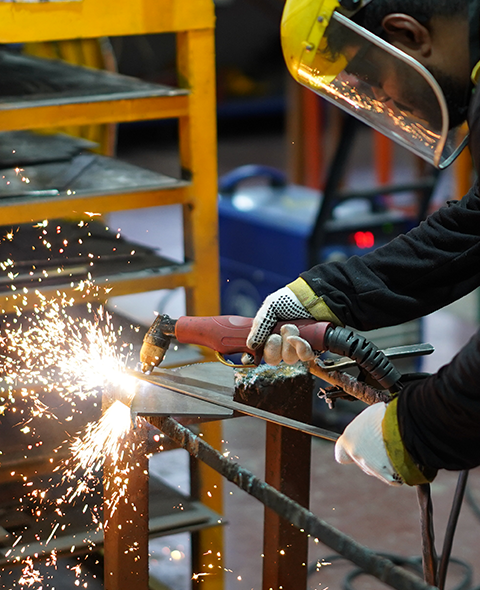
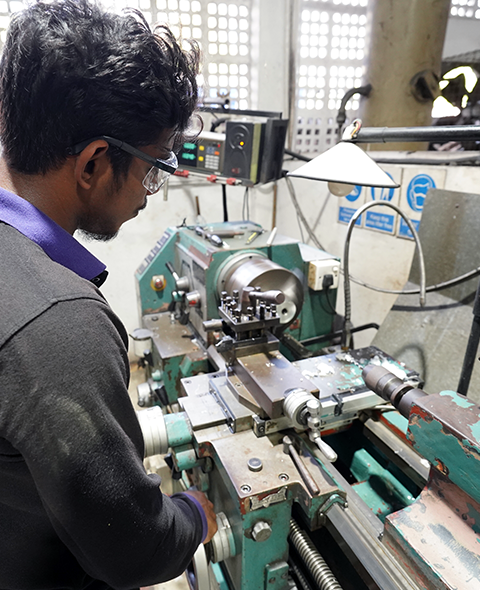
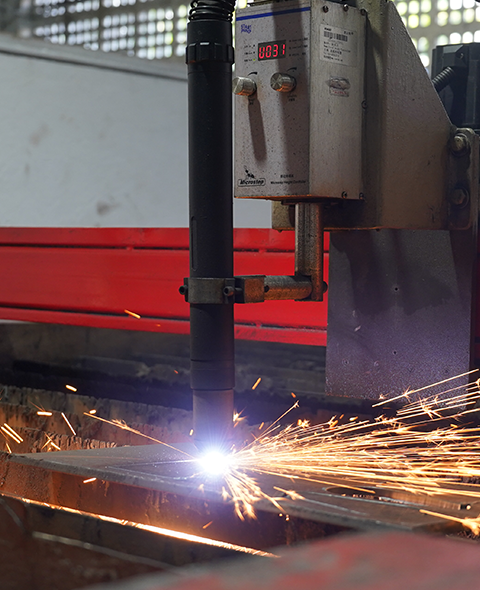
THE DASHBOARD
A vehicle's dashboard consists of around 20 to 40 different visible and non-visible parts. Parts such as air vents, display screens, instrument clusters, airbags, and some switches are reused in the new right-hand drive dashboard, however, many need to be entirely reverse-engineered using advanced 3D scanning technology. These parts undergo rapid prototyping before being manufactured by 3D printing, fiberglass or plastic injection processes. When creating a new dashboard component, several design and production elements are considered, such as the component's physical properties (structural integrity). If the component is upholstered, it must match the rest of the vehicle's trim, likewise, if it is a visible component without upholstery then its exterior finish must match the original OEM look and its UV rating must be considered if it will be exposed to sunlight.
THE HVAC SYSTEM
Our team needs to fully reverse engineer the Heating, Ventilation, and Air Conditioning system as the blower and distributor units must be relocated from their original location on the right-hand side behind the dashboard to the left-hand side to accommodate the vehicle conversion. To achieve this, a combination of reverse engineering and mechanical engineering expertise is utilized to design all the necessary modifications to the HVAC system. Prototype designs are tested using 3D printing technology before we proceed to manufacture both plastic and fiberglass components.
WIRING LOOM
The Electrical Engineering team and auto electricians work together to redesign, modify and test all wiring looms, which include the main loom, door switch loom, dashboard loom, engine bay loom and seat control loom. This is done to ensure that all components function perfectly after the conversion process. All wiring modifications are then independently tested as part of our Quality Control processes to meet ADR regulations.
DOOR SWITCH PANEL
As part of the conversion process, it is necessary to change the door switch panels on both the left-hand and right-hand side of the vehicle. This involves a complete redesign of the door switch housing, which includes 3D scanning of the original OEM housing and then reverse engineering to create a new right-hand side housing that can control all four windows, and a new left-hand side housing that can control one window. In addition to this, modifications need to be made to the wiring loom to allow for the control of the windows from different sides. The PCB also needs to be modified to adjust which windows each button controls.
SEAT MODIFICATION
During the conversion process, all vehicles need some degree of seat modification. This modification may include relocating seat control switches, in-seat massaging, heating and ventilation from the left-hand driver's seat to the right-hand driver's seat, and repositioning seats to ensure a correct driving position. In some cases, reupholstering the seats may also be necessary, depending on the client's requirements. This is especially true when a custom or bespoke interior is requested.
STEERING
Autogroup International has designed, developed, and tested a new right-hand drive steering system for all vehicles that undergo conversion. Collectively we have over 30 years of experience and significant mechanical engineering expertise in steering gearbox, hydraulic rack and pinion steering systems, and electronic power steering used in new EV vehicles. With this expertise, we can develop the ideal steering solution for each vehicle platform converted to right-hand drive.
3D PRINTING
The latest 3D printing technologies such as small and large format stereolithography (SLA), selective laser sintering (SLS), and fused deposition modeling (FDM) are widely used in vehicle design. These technologies enable rapid prototyping, creation of masterpieces for molding purposes, and printing of final production pieces.
PLASTIC INJECTION
Autogroup International has nearly a decade of experience in utilizing Reaction Injection Molding (RIM) to produce both small and large plastic components including parts for dashboard and center consoles. We have perfected the use of RIM plastic technology to create mirror-image components with identical characteristics such as rigidity, external finish, and UV protection levels for many of our key conversion components.
FIBERGLASS
Our team of over twenty-five fiberglass technicians, including a small team of highly experienced pattern makers, has been manufacturing high quality automotive components for the last three decades. We specialize in producing right-hand drive dashboards and have perfected the art of developing the initial 'masterpiece' dashboard, creating molds from it, and manufacturing all the required fiberglass components for each vehicle. Many of our pattern makers have been with us for over twenty years, bringing extensive experience to every project.
UPHOLSTERY
The Upholstery team is responsible for the most visible production task in a complex right-hand drive conversion. They focus on upholstering the visible components of the dashboard, center console, door panel armrest, and other panels to ensure a perfect match to the original OEM trim. This includes matching the color, texture, and feel of all upholstered parts. Additionally, the Upholstery team is responsible for all bespoke 'CEO Luxury' interiors, which includes the upholstery of new seats, privacy partitions, side panels, new roof liners, and other externally visible interior components.
WELDING
Our expert welding team is responsible for all metal fabrication tasks, such as manufacturing the dashboard substructure, modifying the firewall, creating the wiper arm mechanism and mounting brackets. All these tasks are designed using the latest CAD software tools by our Engineering Design team. Moreover, the welding team is accountable for all vehicle armoring work for up to B7 protection levels, roof lifts on SUVs (up to 6" higher roof lift) and other fabrication work required for our specialized vehicle projects.
LATHE & MILLING
The Lathe and Milling team produces various components, such as bolts, hose connectors, bushes, and couplers, needed for vehicle conversions based on the plans and specifications developed by our Engineering Design team.
CNC
The CNC team utilizes both 4-axis and 5-axis CNC lathes and steel hardening technology to manufacture specialized steering and firewall components for various converted vehicles. The Engineering Design and Mechanical Engineering teams complete all designs for the manufactured components, and a 3D printing prototyping process is conducted before the products enter production.
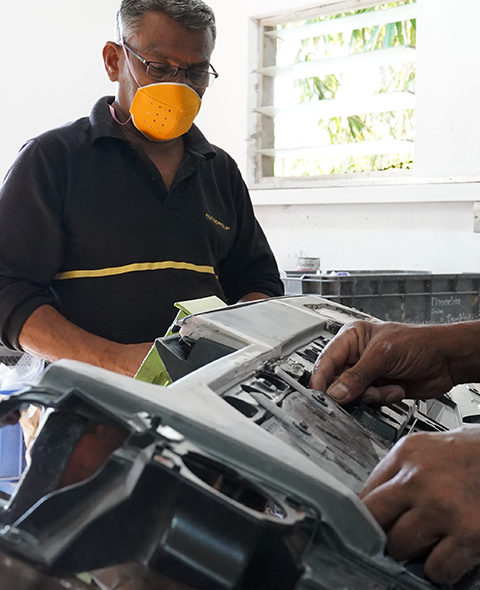
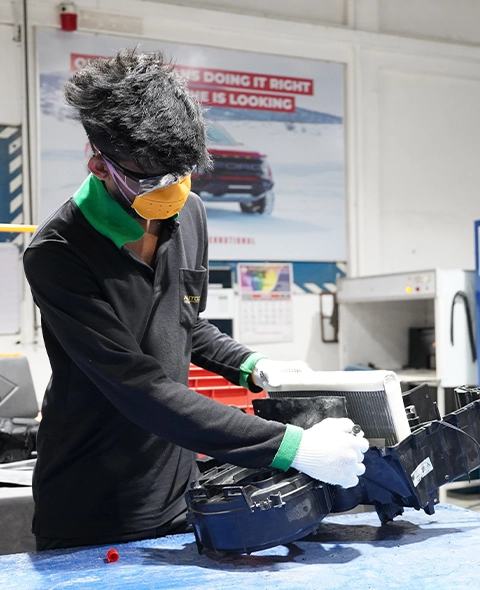
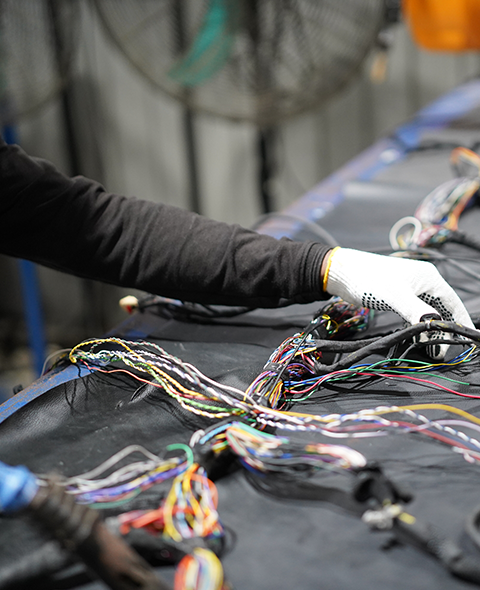
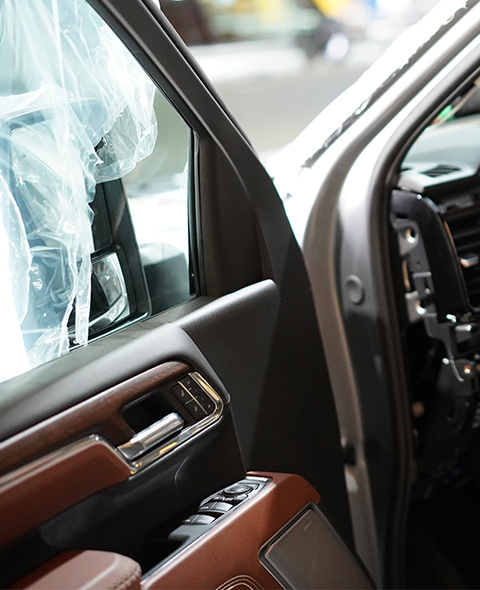
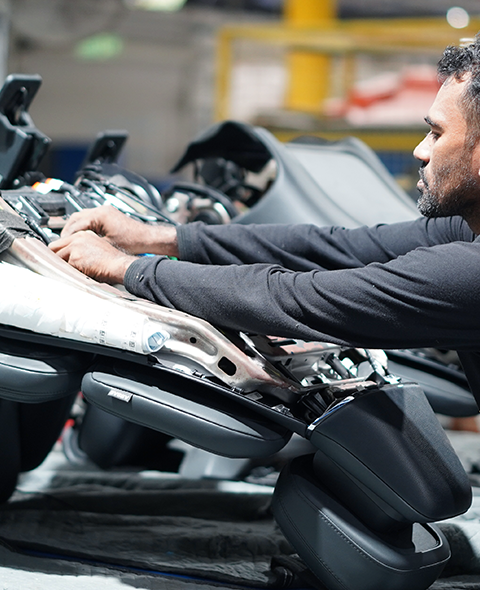
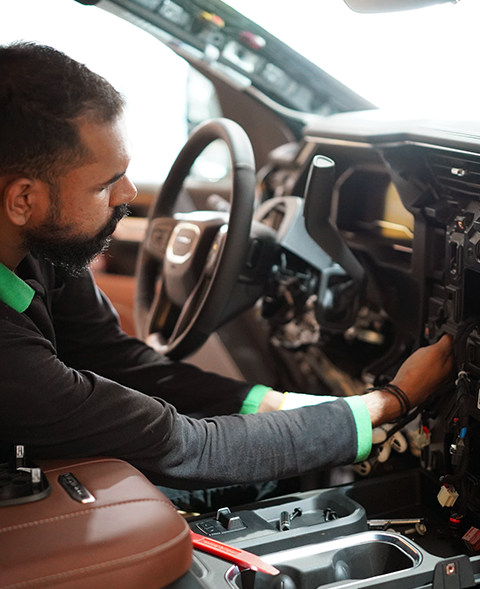
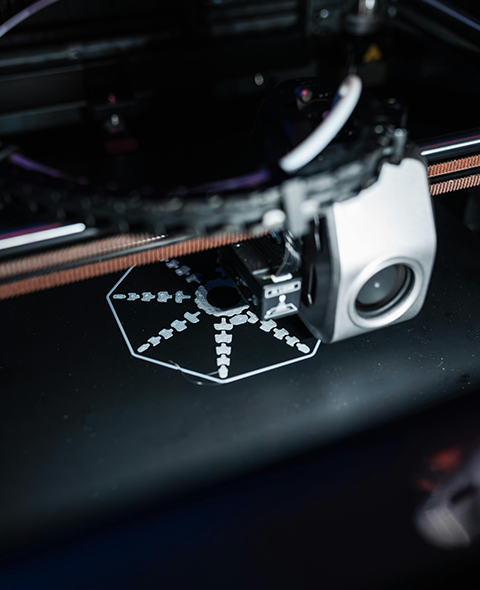
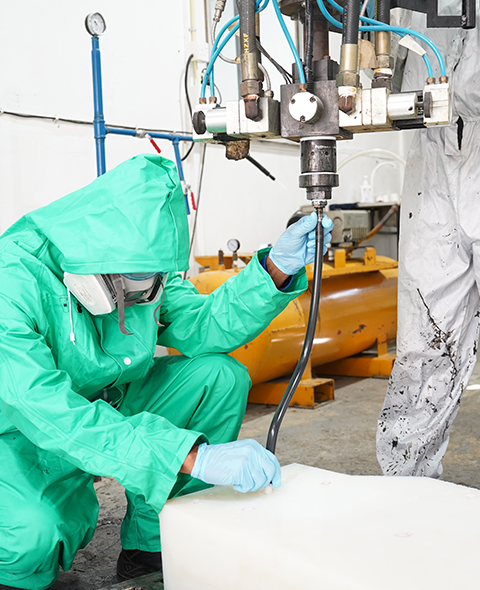

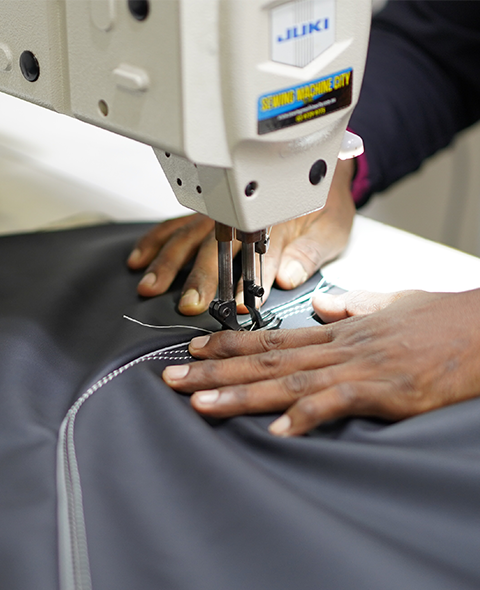
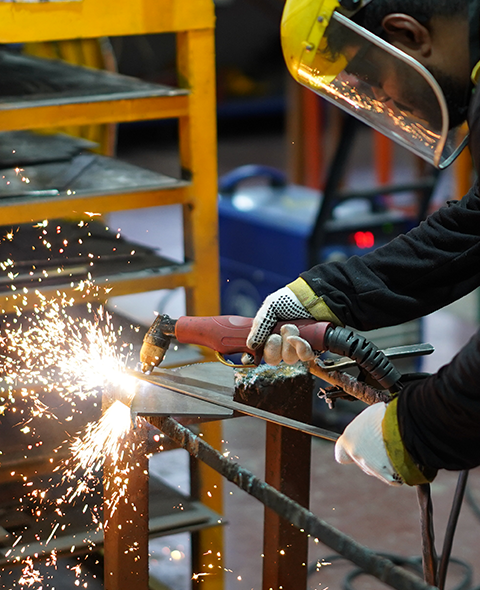
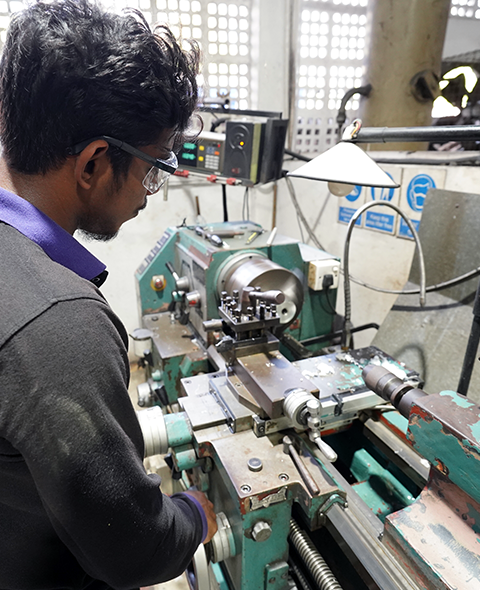
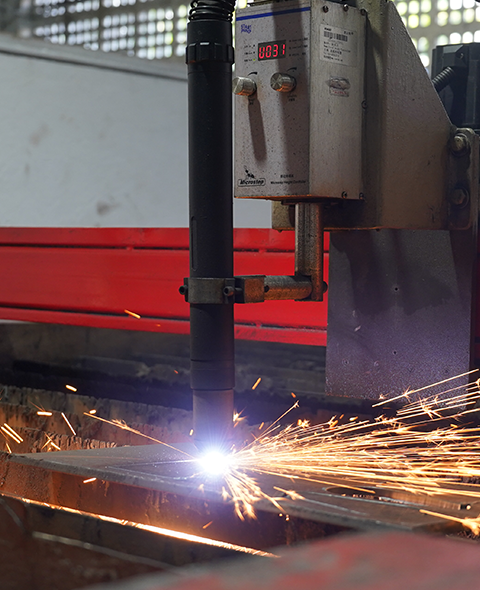
More about
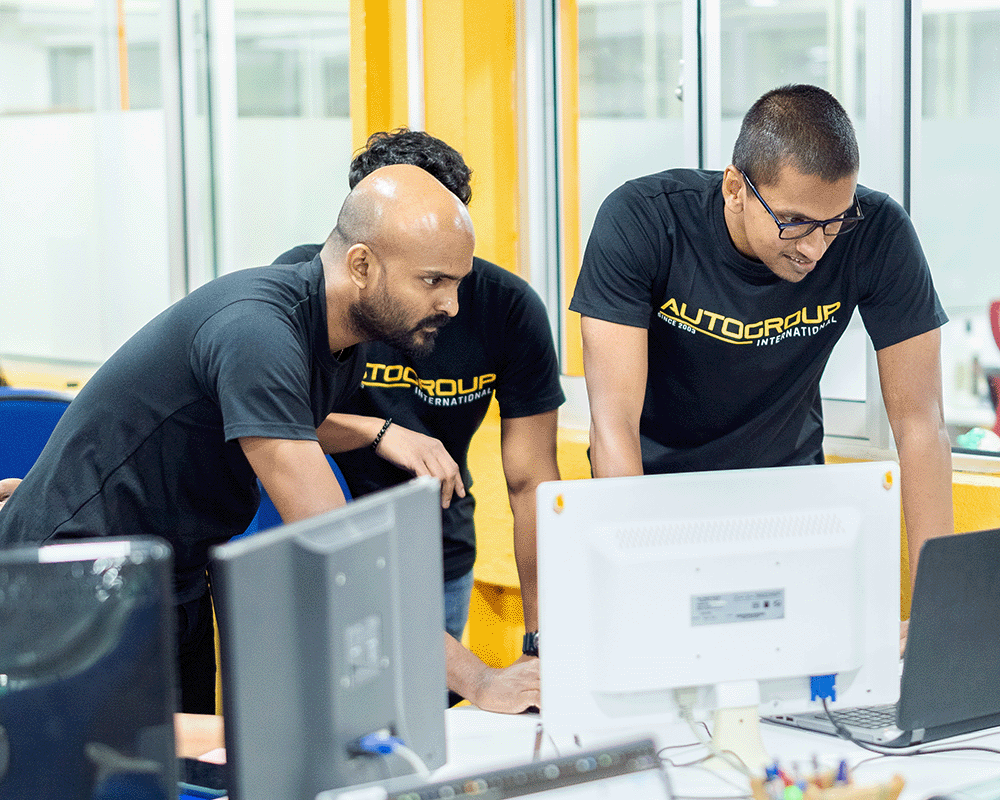
Engineering
The backbone of Autogroup International's conversion process lies in its team of skilled engineers
Learn more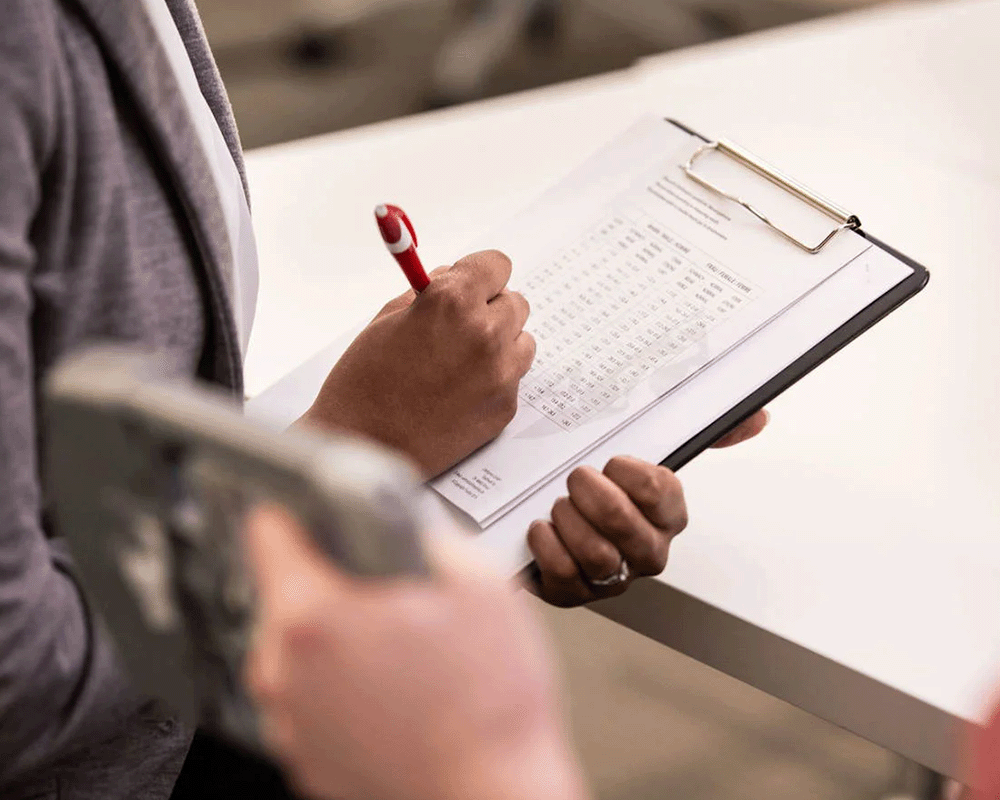
Safety & Compliance
We exceed ISO 9001:2015 Quality Assurance standards, with over 1600 inspection criteria for every vehicle we convert.
Learn more
Conversion
Converting a vehicle from left-hand drive (LHD) to right-hand drive (RHD) is a complex and meticulous process.
Learn more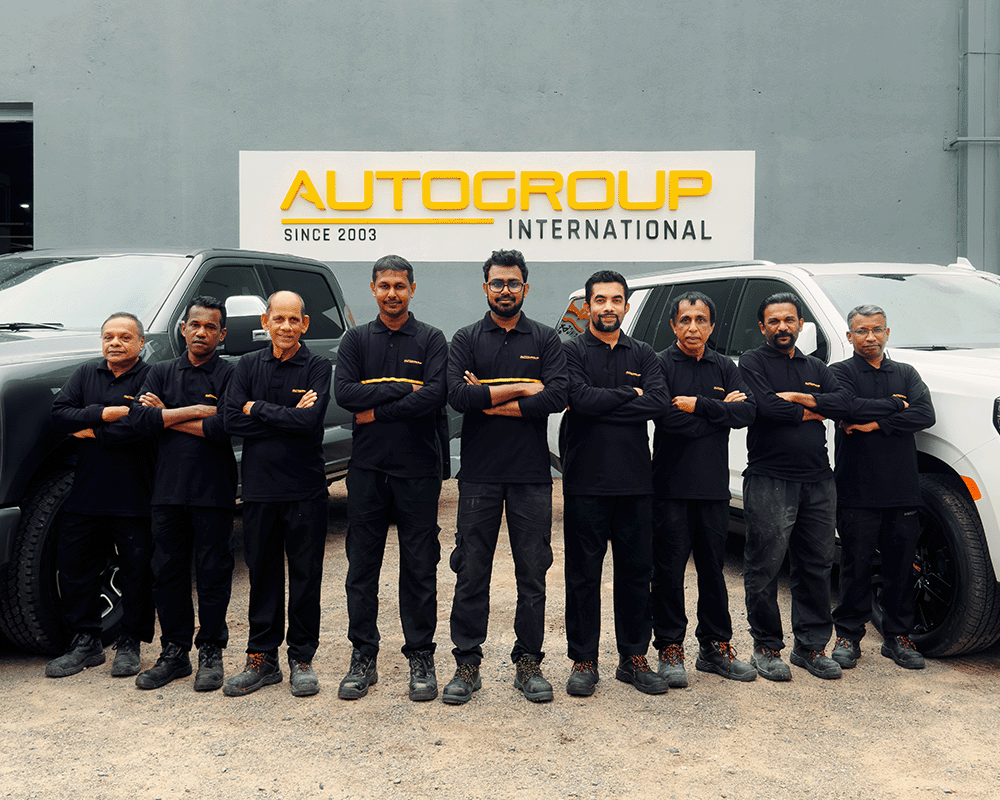
Our Heritage
In 1993 in Australia, an automotive revolution was started which would go on to transform the global automotive landscape.
Learn More